BEWARE!! What follows is
a lengthy recap of the making of my ASHPD. (Portal Gun) May those who choose to
read it have strength!
IN SHORT:
IN SHORT:
-
You can get the 3D printed parts from Jarly Props on Shapeways
-
The wiring was a modified version of Volpin's
-
It is too expensive for you to pay us to make one for you, but read below for tips on how to make your own!
——————————————————————
I’ve been promising a write up
of my Portal costume for a while now, and it’s fair to say that I’ve really left
it for a tad too long. However, good things take time! (don’t think I can dig
myself out of this hole actually….) So forgive me, and thank you to everyone who
has shot questions my way; it has helped motivate me to get this
done!
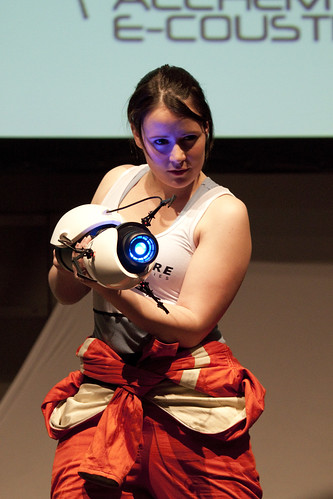
Photo by Troy Belchambers – @greenmonkeytroy on Twitter!
Firstly, for those who don't know, I entered AVCon's 2011 Cosplay
Competition, and won Best Skit.
May you watch it below;
May you watch it below;
It was great fun I tells ya! I
got asked to be in a fair few photos, but mostly people just wanted to have a
photo of the gun. Gah!
Anyway, it all started with the
game. I'm not a massive fan of FPS, but my boyfriend convinced me to give Portal
a try. I think i'll trust his game recommendations a little more from now on,
because I loved it!…which based on my 'logical' progression of thought then
leads on to “I have to make it!”. And so it began.
The research began with the one
and only Volpin. Harrison Krix is a real prop maker, and his ASHPD's are a treat
for the eyes! Needless to say, with neither the tools, nor the talent, I didn't
expect to end up with a prop which could be put alongside his and look the part.
He's just made a Gravity Gun too. You should check it out. http://volpinprops.blogspot.com/
So without the tools, how could
we make a decent replica of everyone's favourite ASHPD?
3D PRINTING OF COURSE!!
3D PRINTING OF COURSE!!
STEP 1 - MAKE THE MODEL
I'm not a 3D
modeler…but my boyfriend Justin is! ( @_R3D_M0NK3Y on
Twitter!)
After having a poke around online, I found a few models which were okay…but none that screamed at me “I am the most accurate ASHPD model you'll ever see!”. (my last poll I asked 'What is the most important thing about a cosplay costume' – 80% said accuracy vs 20% who said being comfortable!) Since accuracy was the goal, it looked like this had to be done from scratch.
After having a poke around online, I found a few models which were okay…but none that screamed at me “I am the most accurate ASHPD model you'll ever see!”. (my last poll I asked 'What is the most important thing about a cosplay costume' – 80% said accuracy vs 20% who said being comfortable!) Since accuracy was the goal, it looked like this had to be done from scratch.
The starting point was a rip
using 3D
Ripper DX, which after getting rid of the rest of the scene resulted in
this.
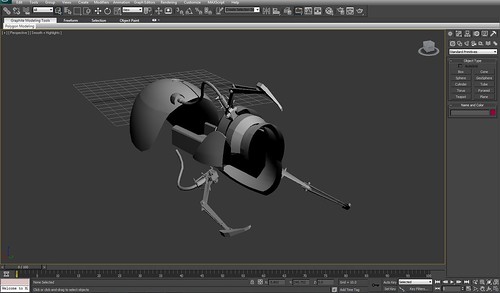
The original plan was to look
through a portal at the player, which resulted in the rip pulling what is being
shown through the portal as it is actual 3D geometry, not just an image.
Unfortunately, while it was whole, the rip was so low poly it was next to
useless. The best is what is shown above, incomplete because it is is actually
what the player always sees in the bottom right of the screen, and therefore for
efficiency, it didn't need to be whole!

Of course this took
some time; I am a very lucky girlfriend.
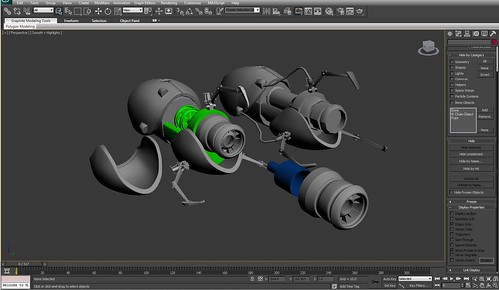
Using the materials guide on Shapeways, the walls were made thin where they could be for price, while still making sure parts which would benefit from thicker walls were given them.
We sent them off to Shapeways and a few weeks later, and in a few different boxes, all the parts arrived!
I talk more about the parts in a previous post.
Chell Portal 2 Costume Progress
They were printed in white strong and flexible.
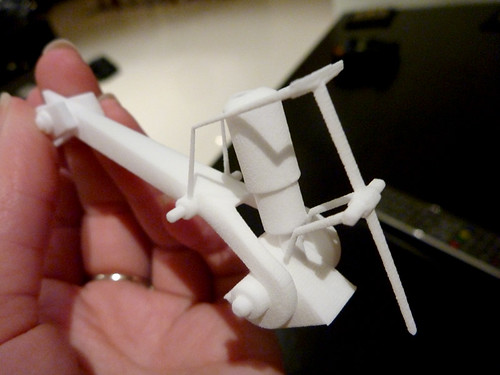
STEP 2 – PREPARE THE PARTS
White strong
and flexible is a porous material, so priming and sanding was in order. We used
a grey body primer to see what we had covered, then sanded, then re-primed, then
sanded. Well, Justin did. Again…lucky.
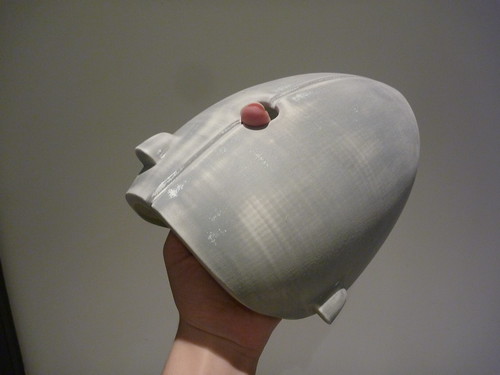
Because the walls
were so thin, we decided slushing some resin around the inside would help to
reinforce the casings. We used Barnes EasyCast which came from Adelaide Moulding and
Casting Supplies. It cures to an off white colour, so it wouldn't look out
of place on the light casings.
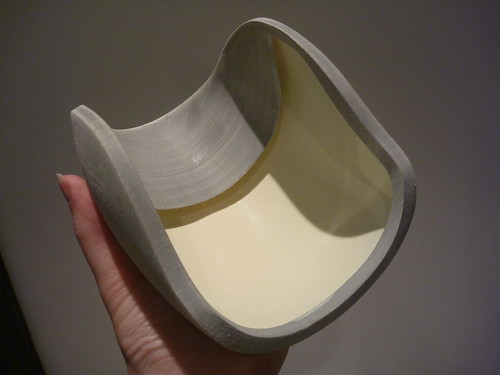
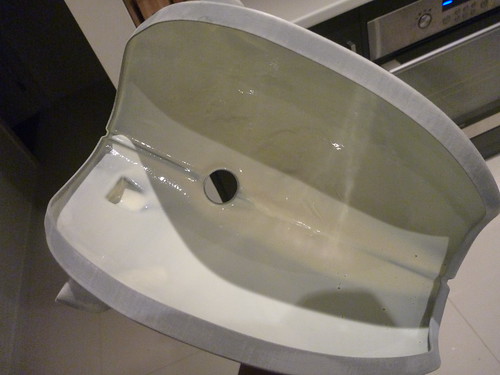
Then came the
painting, courtesy of Games Workshop paints. We went through quite a few Skull
White and Chaos Black cans; the guys in the store seemed completely bemused that
a girl was coming in so often for base coat paint. I'm clearly painting an army
of pure win. :D
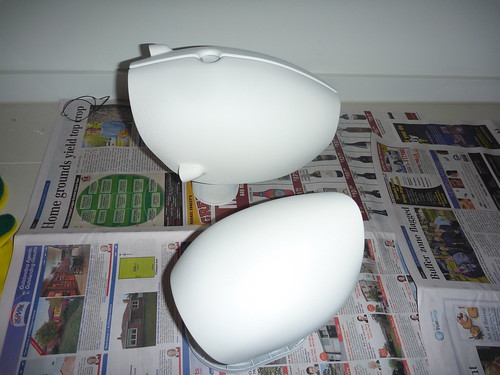
Again with the fine
grit sand paper and a few more light coats of paint and the casings were ready
for waterslide decals and a clear gloss finish.
The other components however, were not.
The other components however, were not.
Under the rear casing
you will find PVC storm water pipe…and a very bad builder's bog job by me!
After some hack saw
cutting, then measuring, then some more cutting, the pipes got to the stage
where they could be joined (with cloth tape of course!) and married with one of
the tube ends with builder's bog. Now this stuff is great, but it stinks and
makes a mess when you sand it!

After a quick test
fit with the tray which sits under the glowing tubes, everything got bogged
together!
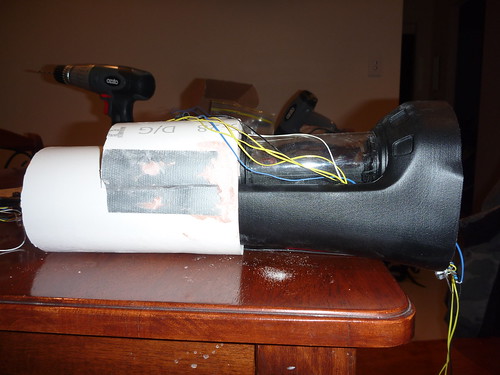
Then the sanding
began. There is an enormous amount of sanding to be done when making props i've
discovered…

I didn't bother making it perfect though; it can't be seen and there are much more important things that need my time…like eating apples and drinking alcoholic beverages. (drink responsibly!)
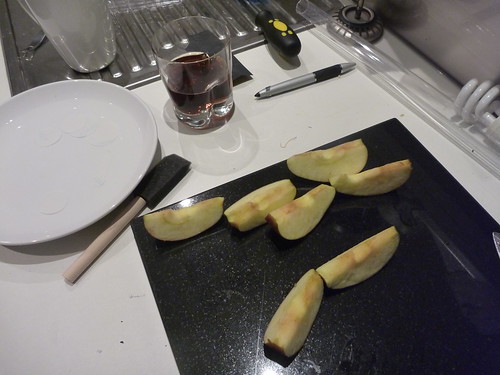
The handle at the
back is actually a kitchen drawer handle, and it's attached to a storm water cap
that sits nice and snugly over the end of the storm water pipe. Perfect!

All black parts were
painted several times in Chaos Black, then received a final few coatings of a
clear satin to finish.
The perspex tubes fit
perfectly in to the 'tube end'
parts; the outer tube has in outer diameter of 50mm, inner diameter of 46mm, and
the smaller tube for the inside has an outer diameter of 19mm. I bought a cheap
lightsaber ripoff, removed the diffusing film and used it in the inner tube.
Originally we'd tried sanding the inner tube with a really fine grit wet rub,
but you could still see the scratches.

The barrel part and the top indicator
(hole in the back casing) were diffused using 2mm acrylic which was wet rubbed
(scratches didn't seem to be a problem with the sheet acrylic, just the perspex
tubes…) then a water slide decal with a grill was transferred to the top. The
adhesive didn't work so well, but once the parts were put together, there wasn't
any room to move anyway!
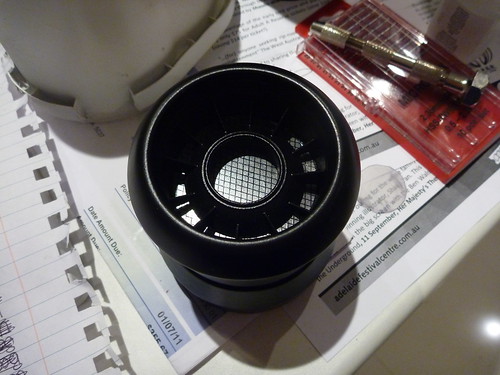
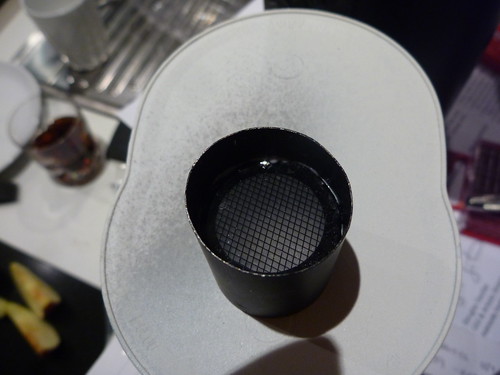
STEP 3 – WIRING
Now I am not an
electronics engineer, but I got the grandpa to explain a few things to me. A few
trips to Jaycar later and I had this mess. Spaghetti! Yum!

That's right. Me make
circuits.
You can hopefully see the circle plastic discs; these had 5mm holes drilled out of them, and the LED's fit in snug. To make sure they weren't going anywhere (because I can't get them out so easy now!) they got a little aquadhere love.
You can hopefully see the circle plastic discs; these had 5mm holes drilled out of them, and the LED's fit in snug. To make sure they weren't going anywhere (because I can't get them out so easy now!) they got a little aquadhere love.

By this stage, the
convention was a mere 2 weeks away, and there was video editing, boot finishing,
set constructioning and practicing to go. Needless to say, time for sleep was
becoming scarse.
I had ordered a
soundboard from replicaprops.com, but alas my electronics skills had failed me
and I didn't get it working for the convention. I have futureproofed though, a
speaker is at the ready at the front of the gun when electronics skills are up
to the challenge.

STEP 4 – PUT IT ALL TOGETHER!
This is around the
time where I started to realize just how good it was coming out and got teary.
It may have been the lack of sleep and nervousness, but I didn't care!
The back casing
needed to effectively 'hover'; so the larger acrylic tube made for a good
support. It did a good job, but I didn't so much. Lots of Araldite and measuring
incorrectly later, and the support was complete! (such a mess!)

A Berocca tin also
featured as a support for the back indicator light.

Pretty much the whole
thing is stuck together with Araldite. Yep.
The last thing to do
was make the wires from the back casing to the claws. These are made from
armature wire, with heat shrink around them. Easy, flexible, light, and lucky
for me relatively cheap!
STEP 5 – WIN!
The day was this
surreal blur of nausea, shaking from sleep deprivation and shifting weight
trying to tell my body I didn't need to go to the toilet. That was scary.
Many a thanks needs
to go out to my boyfriend Justin. Without him, none of this have been able to
come to fruition. I owe many an hour in return for time spent on my cosplay
projects with me, and more again in sleep lost.
Thank you Justin. Please let me know how I can pay. ;p
Thank you Justin. Please let me know how I can pay. ;p

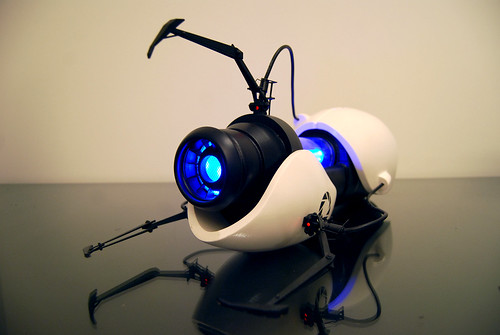
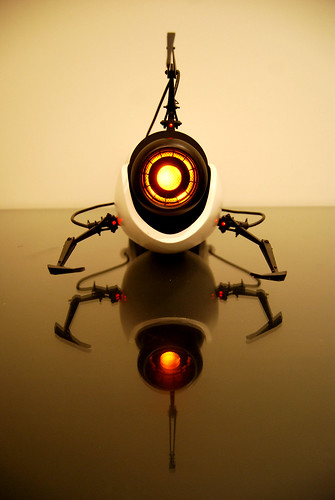
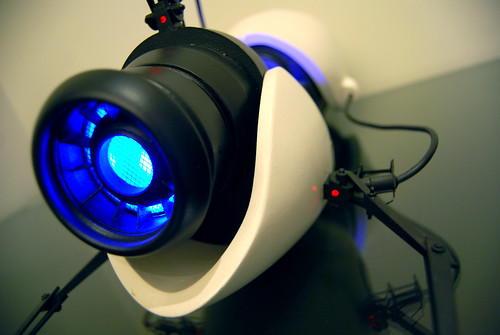
Photos by Justin!
In conversations about AVCon, i'm now 'The Portal Chick', which doesn't bother me.
Actually, i'm just impressed that i'm remembered for anything at all!
Now I just have to
come up with something bigger and better for this 2012.
Time to go see what Justin is playing….
Time to go see what Justin is playing….
0 comments:
Post a Comment